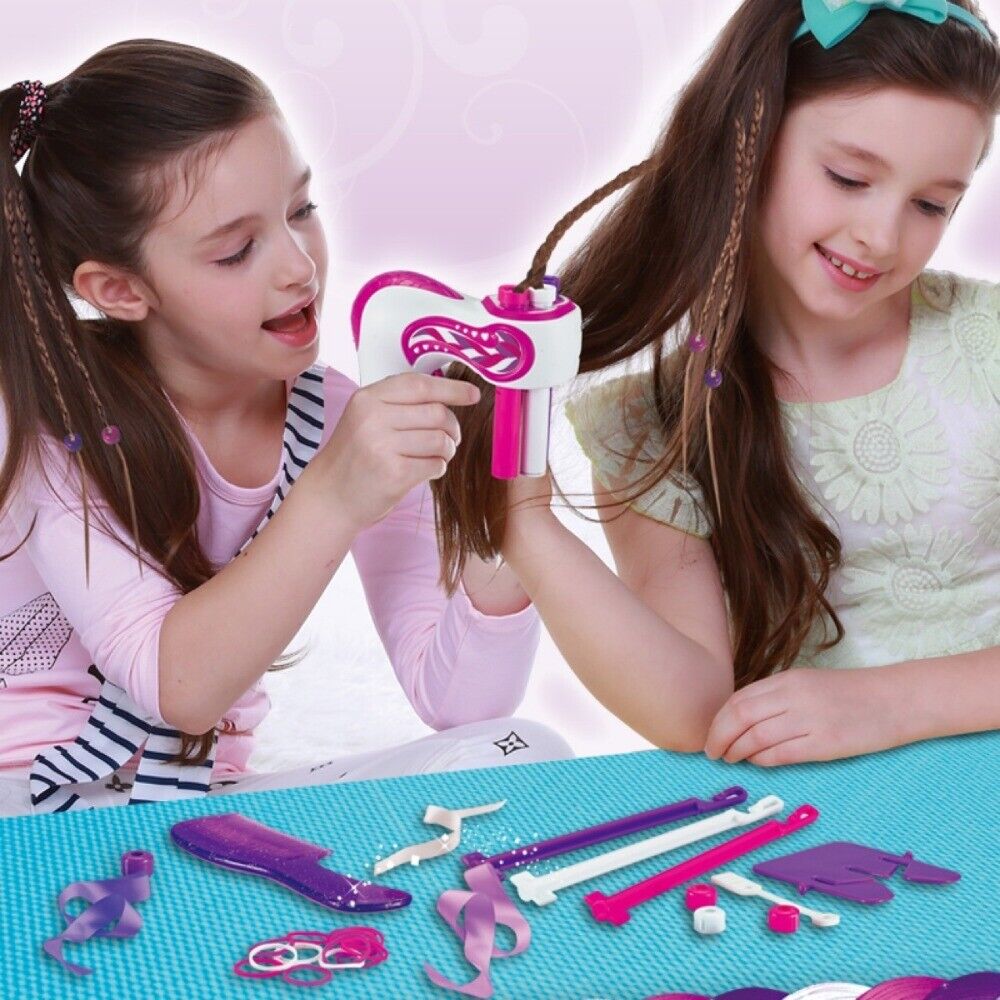
Unraveling the Future : The Hair Braiding Machine
Introduction to Hair Braiding Machines
Hair braiding has evolved from ancient practices into a fashionable art form. Today, the introduction of hair braiding machines(machine à tresse) revolutionizes the way hair styling is approached. These innovative devices utilize advanced technology to create stunning braided hairstyles quickly and efficiently. With the ability to produce various braids, these machines appeal to both hair professionals and enthusiasts alike. The rise of the hair braiding machine signifies a shift in modern hairstyling techniques.
The desire for beautifully braided hair has never waned. Many people appreciate the aesthetic appeal of a well-executed braid. However, mastering the skill of braiding requires time, patience, and practice. Traditional braiding techniques can be labor-intensive and challenging for many. This is where the hair braiding machine shines. It automates the braiding process, significantly reducing the time needed to achieve gorgeous results.
Moreover, hair braiding machines come equipped with various features. These machines can create multiple types of braids, including Dutch, French, and box braids. Additionally, they cater to different hair types and textures. As a result, versatility becomes a hallmark of these machines. The ease of use further enhances their appeal. Anyone can operate a hair braiding machine with minimal instruction. This opens up new avenues for creativity and styling.
Understanding How the Hair Braiding Machine Works
The hair braiding machine operates through a series of automated functions. Initially, users must prepare the hair by detangling it thoroughly. Next, the machine requires a specific amount of hair to be fed into its mechanism. Equipped with sensors, it can detect the hair type and adjust its settings accordingly. This ensures that the machine delivers optimal results for each user’s unique hair texture.
Once the hair is properly positioned in the machine, the braiding process begins. Users can select their desired braid style from a digital interface. With a single press of a button, the machine starts weaving the hair into intricate patterns. The speed and precision of these machines are impressive. Considerably faster than manual braiding, they offer consistent results every time. Moreover, most models feature customizable settings, allowing users to enjoy personalized braiding experiences.
Once the braid is complete, the machine releases the finished product seamlessly. Users can then secure the braid using various accessories, such as bands or clips. They can also add decorative elements, like ribbons or beads, for an added flair. This flexibility enhances the overall styling experience. Moreover, many hair braiding machines come in portable designs. This portability allows users to carry their machines wherever they go, ensuring stylish hair is always within reach.
The Benefits of Using a Hair Braiding Machine
Using a hair braiding machine comes with numerous benefits. First, it drastically reduces the time spent on braiding. Traditional methods can take hours, especially for intricate designs. Conversely, automatic machines can complete styles in a fraction of the time. This efficiency is a game-changer for busy individuals seeking stylish solutions.
Next, these machines enhance accessibility. Individuals lacking braiding skills can easily operate them. This allows everyone to achieve beautiful braided hairstyles without extensive training. Furthermore, hair braiding machines cater to a wide range of users. This includes hairstylists looking to expedite their services and individuals wanting to create personal looks at home.
Furthermore, hair braiding machines promote creativity. Users can experiment with different styles effortlessly. With a few button presses, they can switch between braid types. This encourages exploration into various trends and patterns. Users can also mix and match different braids, creating unique styles tailored to their preferences.
Additionally, hair braiding machines are consistent in their results. Unlike manual methods, which can vary based on skill level, machines produce uniform braids every time. This reliability boosts user confidence and satisfaction. Lastly, these machines often come with built-in safety features. Such features ensure user protection during operation, making them great for all ages. Overall, the advantages of hair braiding machines are numerous and diverse.
Popular Types of Hair Braiding Machines
The market offers a variety of hair braiding machines suited for different needs and preferences. For example, some machines specialize in traditional styles like French and Dutch braids. These machines are designed for users who prefer classic looks. They often feature simple and intuitive controls, making operation a breeze.
On the other hand, some machines focus on complex styles. These sophisticated models can create intricate designs like fishtails or waterfall braids. They typically come with advanced technology, allowing for customizable settings. Users can even save their favorite configurations for quick access later. This capability appeals to professional hairstylists and dedicated hair enthusiasts.
Additionally, some hair braiding machines cater specifically to children. These models feature fun designs and vibrant colors. They often include playful accessories and interactive interfaces. As a result, children feel excited about hair styling. These machines encourage kids to express their creativity while learning about hairstyling.
Moreover, emerging technologies are leading to new innovations in hair braiding machines. Features like touchscreens, mobile app integration, and voice commands are becoming more prevalent. These advancements enhance user experience and make operating machines even easier. Portable designs are also on the rise. Users can take their hair braiding machines on trips or outings, ensuring they always have stylish hair. Each type of machine serves a unique market segment, enhancing the overall appeal of hair braiding technology.
Essential Features to Consider When Choosing a Hair Braiding Machine
Selecting the right hair braiding machine requires careful consideration of several essential features. First, users should evaluate the machine’s versatility. The ability to create various braid styles is crucial. A versatile machine can accommodate different user preferences and hair types. This ensures that the machine is more valuable in the long run.
Second, users must assess the ease of use. Look for machines with intuitive interfaces and clear instructions. A complicated machine can deter users, particularly those new to hair braiding. Simple buttons or touchscreen controls enable seamless operation. Additionally, some machines offer tutorials to guide users through the braiding process. This feature is particularly helpful for beginners.
Another important factor is the machine’s speed. Some models can braid hair in just a few minutes, while others may take longer. The shorter the time required, the better, especially for busy individuals. Check reviews or demonstrations to gauge a machine’s efficiency. Consumers should also consider the design and portability of the machine. A compact, lightweight machine is easier to store and transport.
Moreover, safety features should not be overlooked. Automatic shut-off functions, comfortable grips, and child-safe designs enhance user security. Lastly, warranty and customer service are critical aspects. A good warranty provides assurance of product quality and reliability. Prompt customer service is also essential for resolving any issues that may arise. Taking these factors into account will lead to a satisfactory purchase.
The Future of Hair Braiding Machines
The future of hair braiding machines looks promising, driven by continuous advancements in technology. As artificial intelligence and machine learning evolve, hair braiding machines will become even smarter. Enhanced features like adaptive braiding techniques and personalized styling recommendations are likely to emerge. These innovations will make the braiding process more efficient and satisfying for users.
Additionally, future hair braiding machines may incorporate augmented reality (AR). AR technology can provide real-time tutorials, tips, and styling previews. As a result, users will feel empowered to experiment with different hairstyles before committing. This interactive approach can lead to more creative and personalized hairstyles.
Sustainability is another growing trend. Manufacturers are increasingly focusing on producing eco-friendly machines using sustainable materials. This shift is vital as consumers become more environmentally conscious. Therefore, future hair braiding machines may also feature energy-efficient designs to minimize energy consumption.
Moreover, social media integration is likely to play a prominent role. Users may be able to share their creations directly from the machine. This feature can foster a sense of community among users, leading to increased creativity and inspiration. Finally, as the market grows, more affordable options may become available. This accessibility will ensure that hair braiding machines reach a broader audience, promoting the trend further.
Conclusion: Embracing the Hair Braiding Revolution
The hair braiding machine represents a significant advancement in hairstyling technology. It offers a convenient, efficient, and versatile solution for achieving beautiful braided hairstyles. With numerous benefits, such as time savings and ease of use, these machines cater to various individuals. From professionals to casual users, everyone can enjoy the artistry of braiding without the traditional challenges.
As technology continues to evolve, hair braiding machines will become even more sophisticated. Features enhancing user experiences are likely to emerge, making braiding more accessible and enjoyable. The demand for creativity and personal expression in hairstyling will propel this trend forward. Ultimately, hair braiding machines will solidify their place in the beauty industry.
In summary, the future of hair braiding is bright. With machines making hairstyling easier, individuals can experiment with their looks more freely and innovatively. This revolution invites everyone to explore the art of braiding in fresh, exciting ways. Embrace the hair braiding revolution and discover the endless possibilities that await!